The equipment we use is carefully chosen to produce the most accurate results with the least waste possible. Several of our key pieces of equipment aren’t found anywhere else in New Zealand and allow us to provide high levels of flexibility and increased accuracy across each product we produce.
Core capabilities
Your business is unique, and your success depends on your products performing exactly to your specifications. Our critical and curious thinking combined with class leading technology, bring those products to life, ensuring the highest level of reliability and consistency—because we are invested in your success.
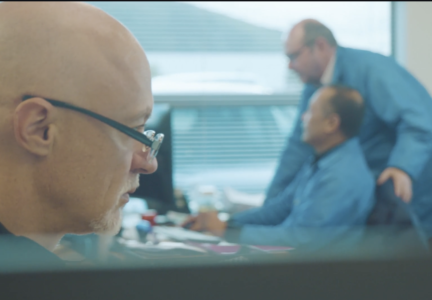
Supply chain & procurement
Reduce lead times and minimise cost working with our experienced supply chain team and leveraging our partnerships with local and international electronic and mechanical suppliers.
Class leading equipment and technology
-
Solder paste jet printer
By using jet printing technology for our solder paste application, we provide high levels of flexibility for our customers with the ability to make changes and modifications to solder paste profiles during a run. If necessary this gives the option to maximise yields by correcting paste deposition within a run. Jet printing negates the need for traditional stencils and is more environmentally friendly as it produces less waste and doesn’t require the production, shipping and storage of traditional stencils. Any change requirements do not need new revision stencils to be produced, simply changes to the software program, saving time and money.
-
Surface mount pick and place
Our SMT pick and placement capability is optimised for lower volume high mix environments. It enables full traceability of all components placed on circuit boards, using individual barcodes for accuracy. Tracking each component within the management software reduces errors and streamlines throughput process. Our equipment can also verify values and tolerances of each component while in process to check for any unacceptable tolerance variations. Thus adding to maximum yield efficiencies and ensuring any new component changes during process are monitored for compliance.
-
Solder reflow oven
Our 6.5m long reflow oven features 20 separate temperature zones, 10 on the top side and 10 on the bottom side of the PCBA. This gives excellent variability and control for fully customisable temperature profiles which are needed with the ever increasing thermal differences of high mass and very small components. This control allows excellent reflow and also minimises the chance of potential thermal damage to individual components.
-
Automated optical inspection (AOI)
With high-quality AOI in place, we’re able to automatically compare 3D models and high-resolution images of a finished product to the product’s Golden Sample and identify any inconsistencies. In addition solder profiles can be checked for compliance with industry standard IPC requirements. Especially useful for product iterations and NPI, our AOI systems mean we can remain flexible and make necessary changes quickly thus reducing process times and ensuring further quality checks.
-
X-ray imaging
With the increased prevalence of bottom terminated components (BTC), process setting and checking for correct solder joints is vital and not possible without an X-Ray machine. Our new technology X-Ray machine allows us to see below the surface to check quality and ensure all connections have been made properly. It is also used as a process check tool to ensure continued in process control and thus high yields. This also provides the capability to check for counterfeit components supply if required.
-
Selective soldering
Our selective solder station provides exceptional quality of solder joints for through hole components. With the multiple and varied requirements of products that we manufacture, the selective solder machine also gives great flexibility to be able to pre define, in software, the specific areas of the PCBA that requires soldering and those that don't. A major benefit is the ability to solder on both sides of the PCBA, even when SMT components are already present on both those sides. Dwell times and control of solder temperature provide exceptional and very repeatable results.
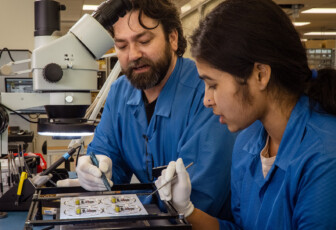
Quality assurance & testing
We apply a high level of attention to detail to our processes, equipment, your products and the customer service experience to ensure quality and accuracy every step of the way. We work with you to manufacture and test products to your industry standards, and have the flexibility and many years of experience to create a process adapted for your needs. We also work with you through any specific testing regimes required for your product, to ensure maximum yields that provide a quality product at minimum cost.
Our employees are certified to relevant international IPC standards and our business to ISO9001:2015 for even greater confidence for our customers.
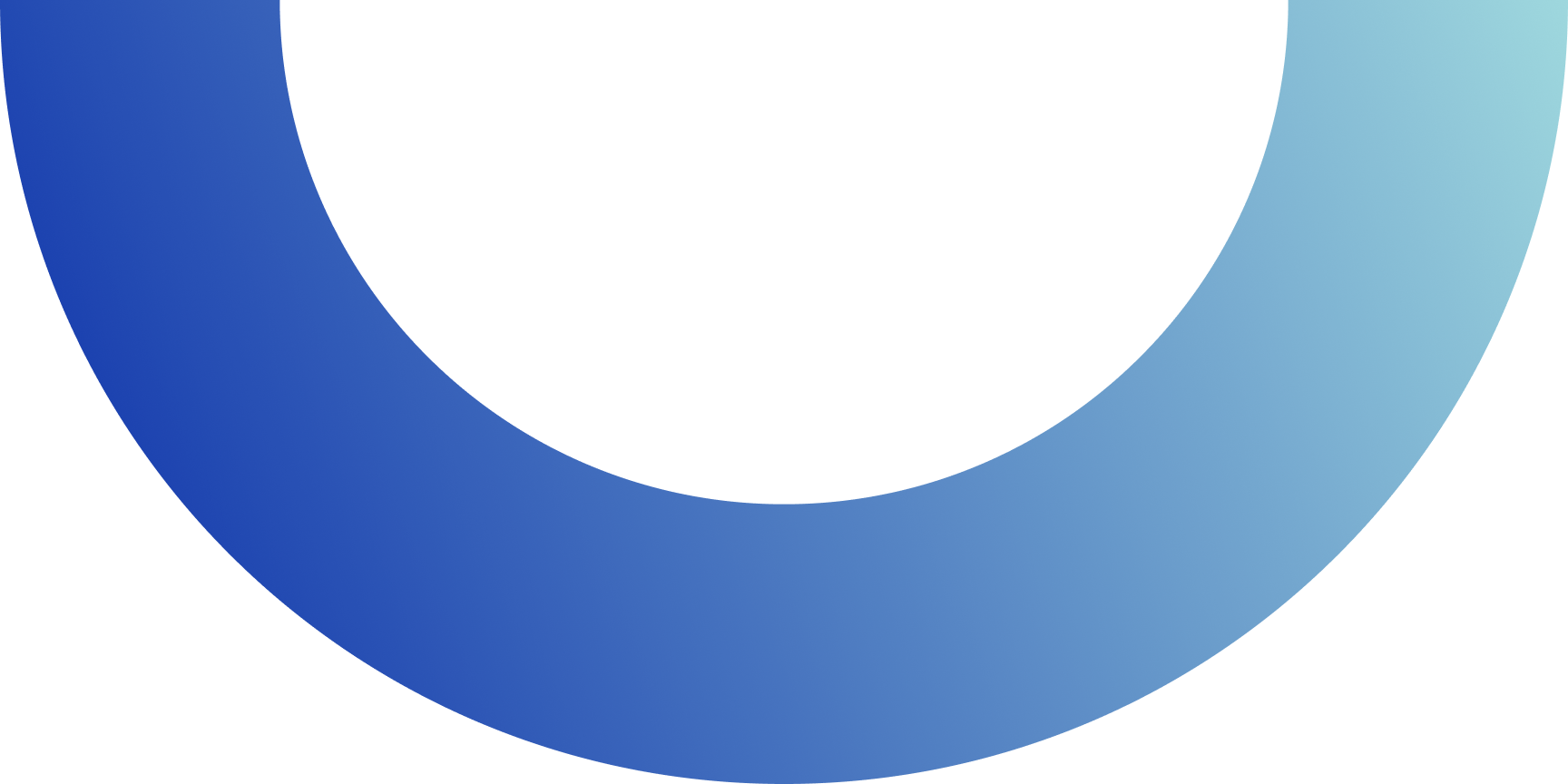
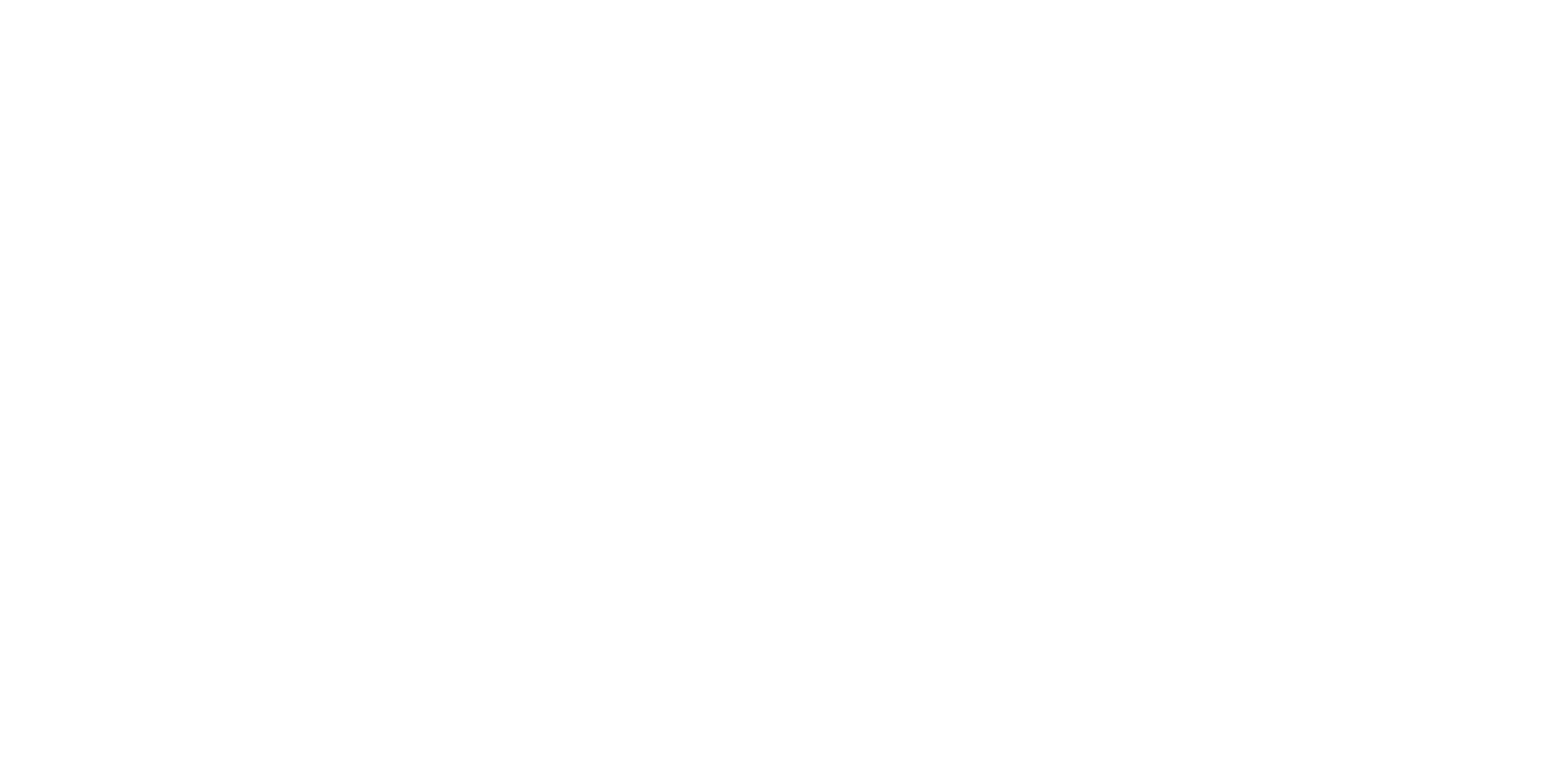
How can we help your business stand out?
No matter what you’re creating, whether it’s complex and high-end or simple and cost-effective, your success relies on your product performing right. And we’re committed to making sure it does exactly that.